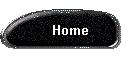
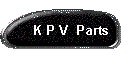
| | K-71 -- K P V Late 1950s through
mid-1970's.
During the formative years of the competitive
karting sport in the 1950's, many different engine prototypes were developed and
tested, but without question, the early power plants developed by the McCulloch
Corporation emerged as the most popular choice among racers and remained the
front-runner for almost twenty years. When McCulloch announced they were halting
production of their kart engine line in 1977, a scramble began for a suitable
heir.
Late
1970's
Following McCulloch's withdrawal one year
earlier, the Yamaha Corporation entered the market in 1978 with what would be
the first of many piston-ported engine designs. This new model was known as the
KT-100. Within a few years, several other manufacturers introduced similar
designs: next came the T-72 from DAP in Italy, followed by the TKM-BT82 from the
Talko Corporation in England and the PCR PP100 from Italy.
Early
1980's
As the popularity of
piston-ported engines continued to rise, a new prototype—the KOMET K71—was
developed in a joint effort between Italian American Motori Engineering (IAME)
head engineer Renato Azzolini of Zingonia, Italy and IAME USA importer Lynn
Haddock of Chattanooga, Tennessee. Mr. Haddock conceptualized the engine and Mr.
Azzolini worked in conjunction with the IAME product development team in Italy
to build the first prototype.
The K71 engine was designed to maximize
performance while complying with existing North American Karting Technical
Committee (NAKTC) guidelines for piston-ported engines. Its design incorporated
two innovative changes from previous 100cc piston-port models: the addition of
large 135cc main bearings, and a billet-slotted connection rod with lower rod
centering. The engine was also the first to be built using heavy-duty components
that were considerably stronger than was necessary to handle the engine’s
power output. This upgrade resulted in an engine that was able to perform for
very long time intervals before needing maintenance.
The original prototype for the K71 was prepared
by using castings from the Komet K30, which was a 135cc rotary valve kart
engine. For the crankcase, two magneto side castings were utilized. This allowed
for the incorporation of the larger 6205 sized main bearings. A special liner
fabricated from a solid sleeve was adapted to fit the old K30 cylinder barrel
casting. The area needed for the inlet port was cut from a solid block, and was
bolted to the casting to provide a mounting area for the carburetor. The head
casting from the K30 was used, and needed only to have the bolt holes
repositioned and a small mechanical change to the combustion chamber. The
crankshaft was developed from a totally new design (without plastic stuffers)
and was fabricated as a one-off unit for testing. It utilized a billet 96mm
connection rod from the IAME racing department’s international Komet rotary
valve kart engine program. The piston assembly was adapted from a Yamaha bike
engine and featured two rings. For the ignition, a then-state-of-the-art
Motoplat unit was imported from Spain.
The prototype engine was assembled, prepared, and
tested extensively on the dyno at the IAME facility in Italy. It was
subsequently shipped to the United States for track testing. The Moroso
Road facility in southern Florida was chosen for its warm winter weather and
considerable privacy. A test was arranged in conjunction with Bill and Todd
Spaude, who provided all necessary equipment. The results from track testing
were very positive, and the decision was immediately made to move forward with
the approval process through the NAKTC, which was supported by both the
International Kart Foundation (IKF) and the World Karting Association (WKA) at
the time. Shortly thereafter, provisional approval was given, and mass
production of the K71 began at the IAME facility in Italy. Following final
counts and inspection, the new engines were cleared for distribution into the
market.
Mid-1980’s
The first race featuring the K71 was held at the
Daytona International Speedway in Florida, and the success of the new design was
confirmed immediately, as teams utilizing it dominated in every eligible class.
Over the coming months and years, the K71 program’s success in the piston-port
arena would continue throughout all divisions of kart racing in both the United
States as well as in Europe, where the FIA-CIK (the European karting
organization) adopted the piston-port design for its international junior racing
class.
1990’s
By the early 1990’s, reed valve engines began
to gain popularity over the older piston-port design in the American market, and
the K71’s use began to decline. Many distributors stopped carrying the engine
and it appeared that the K71 was beginning to fade into karting history.
However—in 1996—the Horstman Manufacturing
Company of California began importing the K71 as a component of their newly
introduced “spec racing kit.” The Haddock/IAME engine design was retained
and paired with a Horstman-manufactured low engagement centrifugal dry clutch
and a spec exhaust system produced by RLV of California. The complete package
was marketed as the Horstman Piston Valve (HPV) kit. The concept was a success,
and was embraced by the IKF, the WKA, as well as many other regional and local
kart racing organizations.
2000’s
Production, distribution, and use of the HPV
engine kit continued until October 2009, when IAME in Italy terminated its
relationship with Horstman and appointed K71 engine designer Lynn Haddock (of
Haddock Limited, Inc. in Chattanooga, TN) as the sole US distributor of the
KOMET program. This action was in response to rising concerns over product
availability and the deteriorating relationship between IAME and the leading US
kart racing organizations.
Shortly after taking over the program, Haddock
Limited introduced a new clutch system for the K71, which is also manufactured
by IAME in Italy. The exhaust pipe kit continues to be produced by RLV in
California.
Today, the K71 engine package continues its long
history of success in the spec-racing arena under its new name—KOMET—and
continues to build on its excellent reputation as a strong and reliable power
package with very low associated maintenance and operating costs.
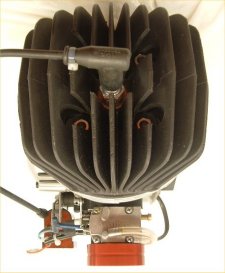
|
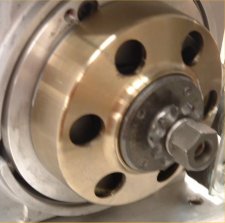
|
|